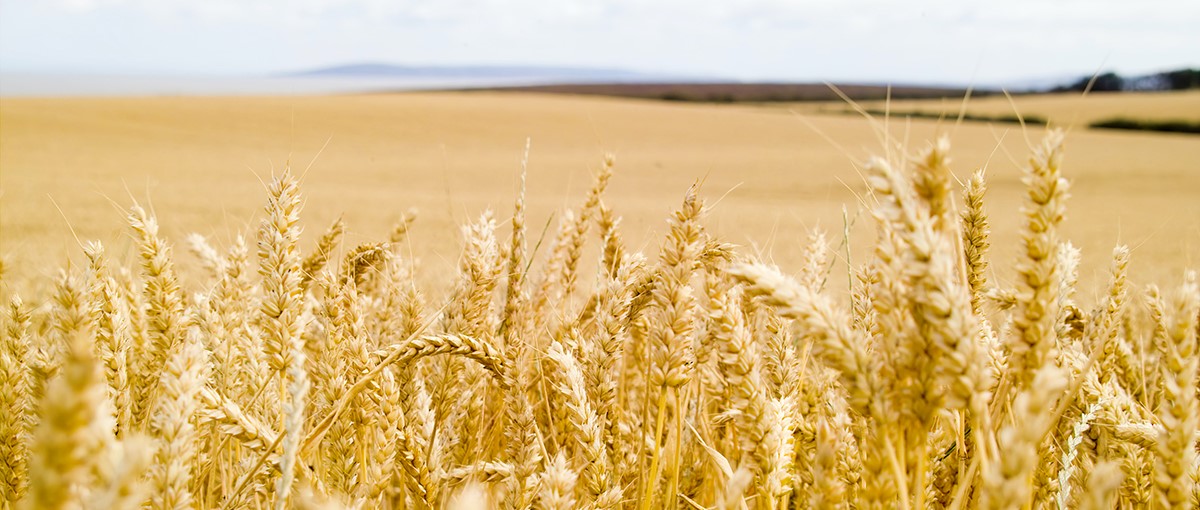
After three years of dedicated work, the Ploutos project, funded under the Horizon 2020 programme, successfully concluded in September 2023.
This initiative was designed to reshape the agri-food value chain, with a primary focus on fostering the transition towards more sustainable systems.
At its core, the project aimed to develop a Sustainable Innovation Framework (SIF) that took a systemic approach to the agri-food sector, leveraging on three key innovation streams: sustainable collaborative business model innovation, data-driven technology innovation and behavioural innovation.
To put theory into practice, the project realised 11 innovation pilots, representing a diverse array of ecosystems across 13 different countries. Adopting a multi-actor approach, these SIPs engaged various stakeholders to implement, test, and assess new innovative solutions and methodologies, including the SIF. In this process, practical insights and valuable lessons were derived, contributing to the continuous transformation of agri-food systems.
The Ploutos SIF was developed by a team of researchers from the Food Sustainability Lab of the School of Management of Politecnico di Milano led by Prof. Raffaella Cagliano. The initial version of the framework was designed at the early stages of the project based on theories and frameworks from the academic and grey literature, which were evaluated together with a panel of experts (representatives of the agrifood sector, universities and research centres, and government organisations). This preliminary version was then enhanced through an iterative cycle encompassing application, evaluation, and refinement, conducted together with the pilots and the experts. In addition to this, a set a practical recommendations and hands-on tools was developed, making the application of the SIF easily replicable.
According to the Ploutos SIF, the innovation process in the agrifood sector starts with the forming phase and is driven by a combination of supply push (e.g., policies), market pull (e.g., changes in consumers’ preferences) and technology push (e.g., introduction of more sustainable agri-food technologies).
The actual process starts when multiple actors come together and agree on a common mission. During this phase, an initial understanding of the changes needed in terms of business models, technologies and behaviours is developed. Integration of the three innovation streams is of paramount importance since sustainability is a systems-level problem that cannot be addressed with siloed approaches.
The second stage of the innovation process, called baseline assessment, requires defining clear sustainability priorities, identifying relevant key performance indicators linked to such priorities and assessing the baseline sustainability performance.
Focusing on the core of the process, the innovation phase, the SIF suggests following an iterative sequence of “understand – define – ideate – prototype – evaluate” to be performed for each innovation stream. One should start from the business model and develop a preliminary version that provides clear answers to questions such as: “How are resources procured and transformed to deliver value?”, “How do products or services meet customer needs and respond to societal challenges?”, “Who are the critical partners and collaborators in value creation?”.
Once a promising business model has been ideated, resources can be allocated to the technological innovation. Key aspects of technological innovations for the agrifood sector include data sharing principles (i.e., ensuring that data are not used against the farmers), interoperability (i.e., connecting different smart farming devices, databases, and information systems), and integration of different technologies, such as traceability systems and carbon credit platforms, to tap into additional revenue streams.
The new business model and the technological innovation will then trigger behavioural interventions to ensure they are successfully adopted. Behavioural innovations can be very wide in scope, going from technology adoption to consumer empowerment and creation of resilient ecosystems.
Solutions developed in each stream are then improved and fine-tuned through iterative cycles until the innovation process is completed.
The last phase of the SIF is the final evaluation that allows to assess the contribution of the proposed innovations to the key sustainability priorities.
The Ploutos SIF was followed by all the 11 pilots and allowed to achieve or even exceed most of the targets set by the pilots, proving to be an effective and easy-to-apply framework for a wide spectrum of agrifood innovations.