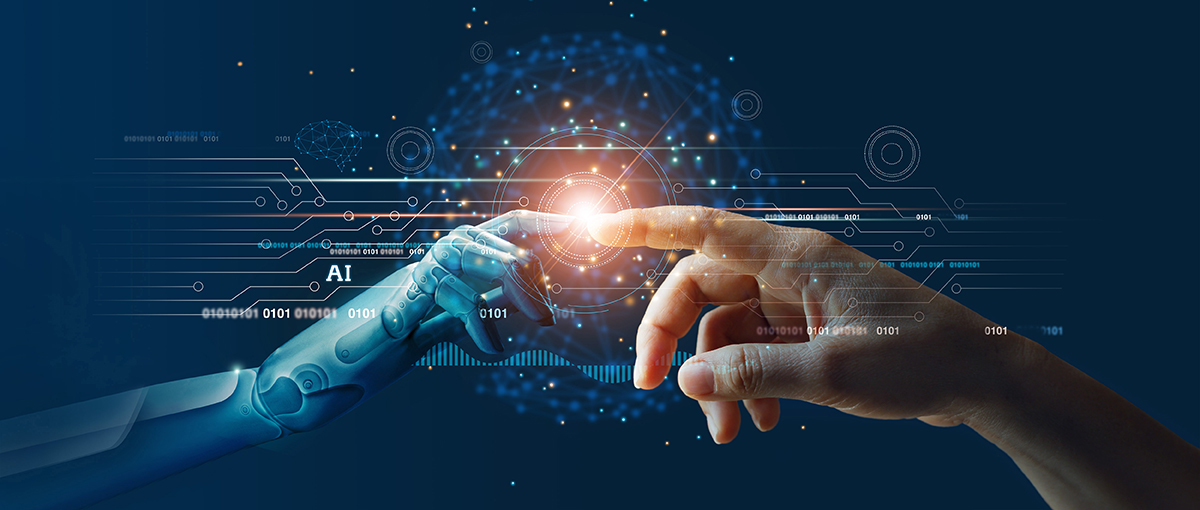
Conversation with Marco Taisch
Professor of Advanced and Sustainable Manufacturing Systems, and Operations Management, School of Management, Politecnico di Milano
Scientific Chairman of the World Manufacturing Foundation
President at MADE, Competence Center on Industry 4.0
Tell us about the path that led to the World Manufacturing Forum: why was it launched, and what are its objectives?
Since first edition of the forum held in 2011, the World Manufacturing Forum is organised yearly by Politecnico di Milano with financial support from the European Commission. In 2018, thanks to Confindustria Lombardia and Regione Lombardia, in order to give stability and guarantee an expansion of activities, we created the World Manufacturing Foundation, which organises the annual event and deals with various initiatives.
The Foundation, created as an open international organization involving regional governments, companies, trade associations, industrial and non-industrial, therefore has the strategic objective of restoring the centrality of the manufacturing sector in the political agendas of various countries.
The main tools put in place are the World Manufacturing Forum, that last year attracted around 1500 people in three days, and the World Manufacturing Report, a yearly white paper that, through a process of consultation with experts from the world of business, academia and policy makers, collects opinions and offers visions for the future on a specific issue, which are relevant to manufacturing, suggesting key recommendations.
In the first edition, in 2018, we addressed the issue of the future of manufacturing as a lever for creating economic and social well-being; in the second, last year, we focused on the fundamental skills required by the sector. And this year, in the event that will take place on 11 and 12 November, we will talk about artificial intelligence.
The 2020 edition of the Forum has a unique flavour, a flavour relating to distance, but also to post-Covid recovery. What kind of edition will it be?
The format of the event will change due to the need for social distancing, but only in part: it will take place at the traditional venue in Villa Erba di Cernobbio with a maximum of 200 participants, with worldwide streaming.
We asked ourselves, like everyone else, what will be the impact of Covid on the manufacturing sector at regional and global level, and to give us an answer we created the “Back to the Future” project (the quote is intentional), new this year.
We “decomposed” the complexity of the problem into 14 sub-themes and created 14 working groups accordingly, each one coordinated by an expert (managers, representatives of the associative world, policy-makers, academics), who were asked to discuss and analyse the impact of Covid on their area of expertise, and to give recommendations.
We have already shared online, with the public, several drafts of documents and videos, produced by these workshops, whose results will be presented on the first day of the Forum, on November 11. On November 12 we will present the World Manufacturing Report.
If I can give a little preview, next year we will talk about digital transformation as an enabler of manufacturing sustainability, thus bringing together the two most important trends in the sector.
We come from the epic situation of Industry 4.0. How can digitisation in the factory world be a competitive advantage for boosting production and starting up again faster?
Before the pandemic, it was “normal” to say that digitisation was the competitive advantage, and that’s the way we characterised the 4.0 industry. Now we have changed the statement: it is no longer an advantage, but a business prerequisite.
During the lockdown we saw how digitisation ensured business continuity for many companies that had already invested in this area. For others, unfortunately, there was nothing to be done.
It was a tragic way of realising, undoubtedly, that it affected those companies which, out of ignorance or inertia, had not paid attention to this technological trend.
In our country in particular, which was slower to adopt new technologies, the pandemic has accelerated the awareness of the importance of digitisation.
Large companies and small businesses: who has the advantage in this fourth industrial revolution?
Large companies have been digitising in our country for some time now, even before the “National Industry Plan 4.0” of 2017. Small and medium-sized enterprises, were, in fact, lagging behind. It was thanks to the plan, and the planned tax incentives, that they became aware of this opportunity for modernisation. Paradoxically, it was by talking about tax incentives that it was also possible to train in the field of technology, and this had a huge impact on the cultural growth of our country on these issues.
It is very important that the national plan has continuity over time, and that it is not a one-off incentive, to enable businesses—especially small ones—to plan and build a training and expertise programme. And today, to do so, they have several tools at their disposal, such as the Digital Innovation Hubs, and especially the Competence Centers. The Politecnico di Milano has put itself in the forefront of this last tool by creating MADE, a competence center that, gathering the skills of multiple departments, coordinates the work together with 44 other partners from the academic and industrial world.
What, in your opinion, are the 3 key words on the evolution of digital transformation in factories over the next 6 months?
First of all “servitisation”, i.e. the development of new business models that are being created thanks to new digital activities carried out in remote industries.
And then the second, “remote” or, if you like, “industrial smart working.”
Finally “resilience”, meaning adaptability, reconfigurability and flexibility of the factory and the supply chain.